Introducing the new Sodick VN Series of linear motor-driven wire-cut EDM machines
For manufacturers that demand the epitome of precision, component quality and production efficiency, Sodick Europe has now introduced the new Sodick VN Series of linear motor-driven wire-cut EDM machines. Presented as a high-quality enhanced range of standard EDM machines, the exceptional new arrival offers all of these benefits along with the added advantage of drastically reduced power consumption and operational costs.
Available in two variants, the exciting new VN400Q and the VN600Q can deliver an astounding 20% decrease in power consumption when compared to standard models. With energy prices at record levels, the new technology incorporated into the new VN Series is a timely welcome for manufacturers. With up to 70% of wire EDM energy consumption used by the dielectric treatment system, the new Sodick VN Series solves this with a new fluid control circuit that reduces the energy needed to drive the dielectric processing pump. Utilising an inverter to control the vertical flushing flow rate during machining, a 20% reduction in power consumption during machine standby is achieved.
As well as reducing power consumption, the newly developed energy-saving pump is integrated into the dielectric tank and, along with the LN3W/LP3W Power Supply unit, the Sodick VN Series significantly improves nozzle flushing performance to amplify the open cutting speed by up to 15%. This simultaneously provides end users with higher productivity levels and reduced energy consumption. This is all complemented by an ‘Intelligent Monitoring Circuit’ that monitors the vertical flushing flow rate to further optimise pump drive energy for flushing.
Further contributing to the efficiency of the Sodick VN Series is the linear motor drive system with linear scales. Providing precise high-speed axis motion that is wear-free, the extremely responsive speed, precision and repeatability can be maintained for years to come. This performance is further enhanced by the latest K-SMC motion controller that governs axis movements and meticulously tracks spark gap adjustments. The result is an ultra-fast response time of between 0.4 to 1 micro-seconds, which is also credited to the absolute linear glass scales that have eliminated the need for referencing. Supplementing this speed and precision is the strategic integration of ceramic for vital components such as the upper and lower guide assemblies and table guide supports.
With regards to daily running, the Sodick VN Series simplifies operational use of the end user with a four-sided workstation, slide plate maintenance to reduce maintenance and retain consistent precision as well as a triple filtration system that purifies fluid, prevents sludge build-up, reduces maintenance requirement and extends the machine uptime. In addition, the VN Series incorporates Sodick’s industry-leading automatic wire threading unit, an innovative wire collection system and offers improved ergonomics for the end user with a machining tank that is 60 mm lower than the work stand upper surface. This improves accessibility for the operator and makes it easier to load and unload components.
From a specification standpoint, the smaller VN400Q has an X, Y and Z-axis travel of 400 by 300 by 230mm with a 635-litre work tank that has dimensions of 860 by 740mm (WXD) and a maximum workpiece weight of 500kg. In comparison, the larger VN600Q provides an X, Y and Z-axis travel of 600 by 400 by 310mm with a 970-litre work tank that has dimensions of 1150 by 840mm (WXD) and a maximum workpiece weight of 850kg. both machines offer a U and V-axis travel of 90 by 90mm, a taper angle of +/-15 degrees, a wire diameter from 0.1 to 0.3mm with a tension of 3 to 23N and a maximum wire speed of 420mm/sec. As with all Sodick machines, Sodick Europe can offer a complete range of optional extras such as Sodick’s in-house developed propriety rotary table system, the AVC high wire alignment option for increased precision for fully automated applications and also the L-cut system that cuts used wire into small pieces for longer production times.
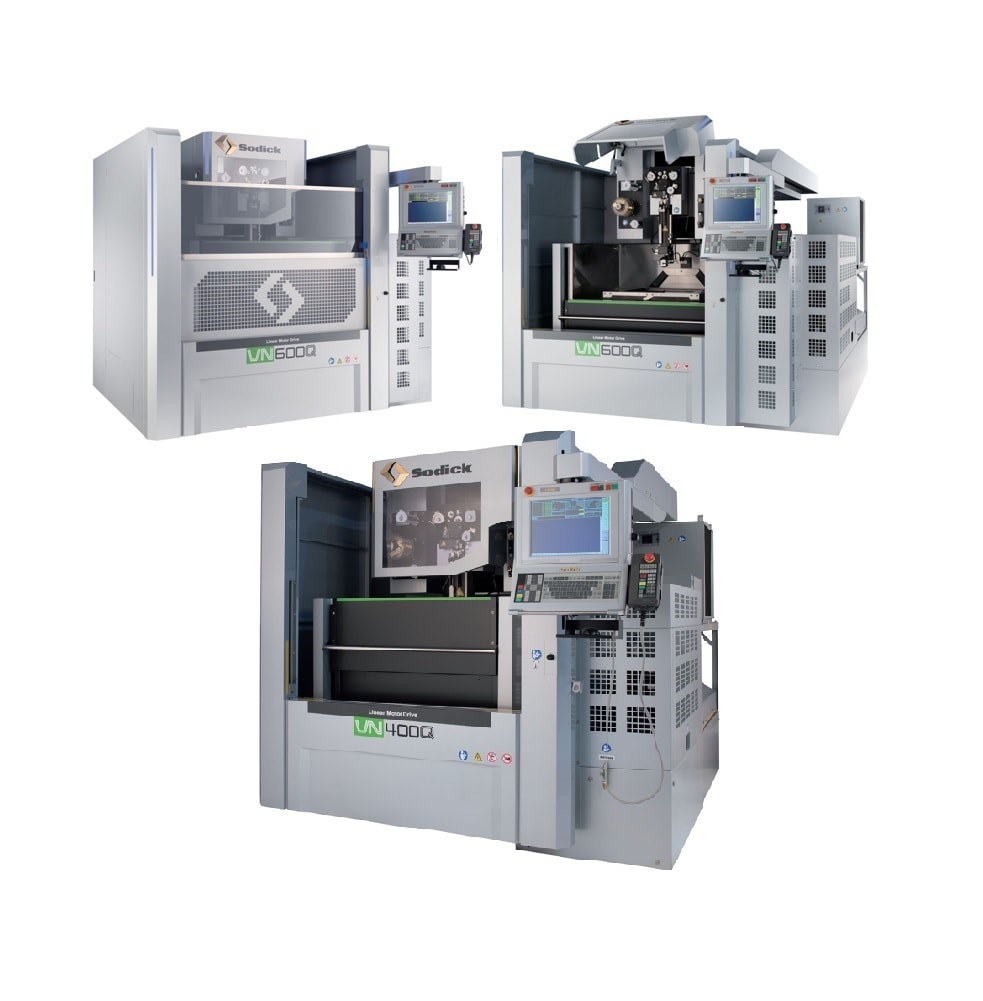